The Retrax PowertraxONE XR tonneau cover system exhibits several common operational issues that require attention from truck owners.
Users frequently report water infiltration problems, motor responsiveness failures, and rail misalignment concerns.
These technical challenges can compromise the cover’s primary functions and lead to potential cargo exposure.
Understanding the root causes and implementing appropriate diagnostic procedures enables owners to maintain peak performance and prevent system deterioration.
The following analysis examines each critical issue and its resolution.
Understanding Water Leakage Issues in the PowertraxONE XR
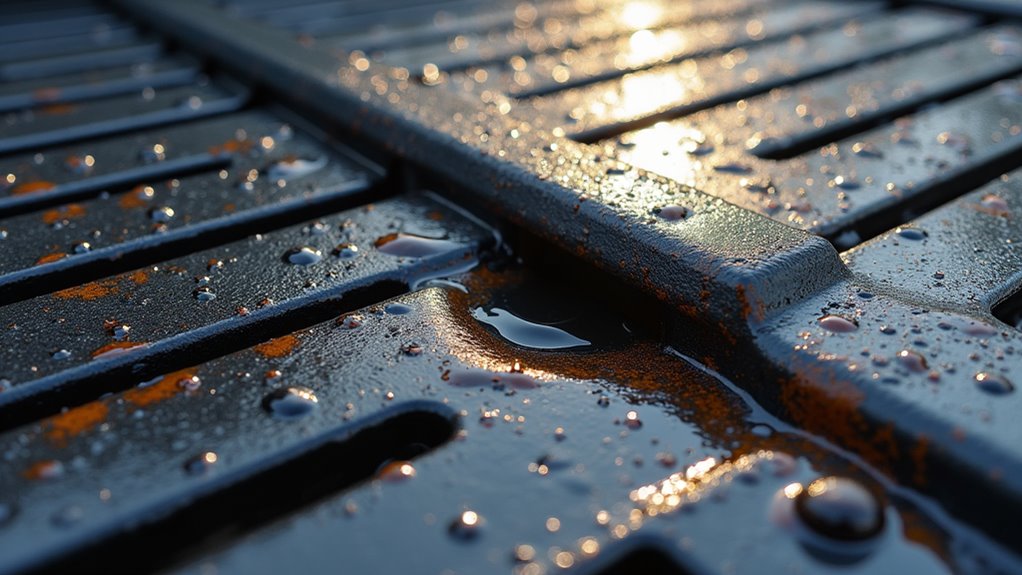
While the PowertraxONE XR offers robust truck bed protection, water leakage remains a common issue that requires careful diagnosis and resolution.
The primary entry points occur at the tailgate and side rail junctions, where inadequate Rubber Seal installation can compromise the Tonneau covers’ waterproof integrity.
Critical inspection points include verifying the presence and condition of foam seals underneath the cover, ensuring proper alignment of components, and confirming that drain tubes are unobstructed and correctly positioned.
Water intrusion typically manifests after rainfall, with severity varying based on installation quality and maintenance.
Users experiencing moisture problems should systematically examine seal placement, verify drain tube functionality, and assess overall cover alignment.
Regular maintenance checks help identify potential issues before they lead to significant water penetration, preserving the cover’s protective capabilities.
Rail System and Track Performance Problems
The rail system’s performance in the Retrax PowertraxONE XR directly impacts the cover’s functionality and user satisfaction.
Track misalignment poses a significant challenge, compromising smooth operation and potentially causing binding issues during cover movement.
Maintaining ideal performance requires systematic attention to several vital factors.
Regular inspection of the tracks helps identify damage like cracks or bends that could impede operation.
Debris accumulation necessitates thorough cleaning of the rail system to prevent operational interference.
Following cleaning, proper lubricating of the tracks guarantees smooth cover movement and reduces wear.
Proper installation plays a key role in preventing track-related issues.
Loose mounting along the edges can lead to misalignment problems, affecting the rail system’s performance.
Users should verify secure attachment points and maintain proper alignment to maximize operational efficiency.
Mechanical and Motor Operation Challenges
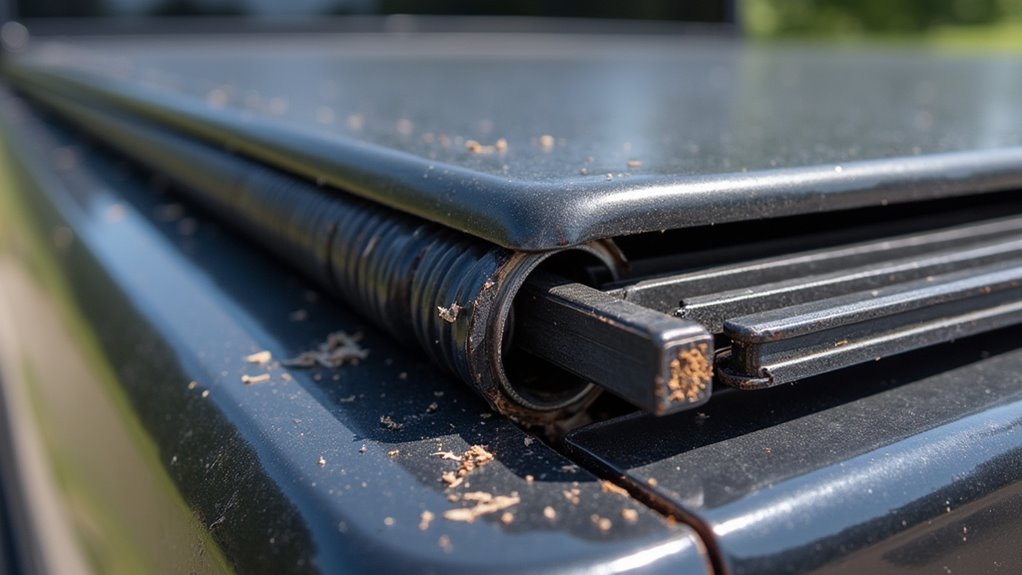
Motor operation challenges greatly impact the functionality of the Retrax PowertraxONE XR system, with unresponsive motors and intermittent power delivery being primary concerns.
Users frequently encounter situations where the motor becomes non-responsive due to insufficient power, requiring thorough inspection of electrical connections and fuse systems.
When the cover exhibits limited movement or sudden stops, this typically indicates binding issues or misalignment within the canister assembly. Stripped gear teeth may also contribute to operational failures.
For diagnostic purposes, implementing a Manual Switch Kit enables direct power testing from the battery, effectively isolating electrical system components for troubleshooting.
After extensive testing, if motor operation remains compromised, replacement with part number RTX79TR may be necessary.
Power delivery issues often manifest after prolonged usage, suggesting potential internal motor deterioration requiring immediate attention.
Seal Integrity and Weather Protection Concerns
Seal integrity failures present significant challenges for Retrax PowertraxONE XR owners, with water intrusion being a primary concern around tailgate areas and between cover slats.
Users consistently report cargo damage from water leakage during even light rainfall, despite properly maintained drain tubes.
The retractable design‘s inherent movement can accelerate seal wear, compromising weather protection more rapidly than fixed covers.
Installation misalignment frequently compounds these issues, highlighting the critical need for precise fitment between the cover and truck bed perimeter.
To maintain peak seal integrity, owners must regularly inspect weatherstripping for signs of deterioration and promptly address any compromised components.
Regular maintenance protocols should include thorough seal inspection, proper alignment verification, and immediate replacement of damaged weather protection components to maximize the cover’s effectiveness against environmental elements.
Installation Complications and Alignment Fixes
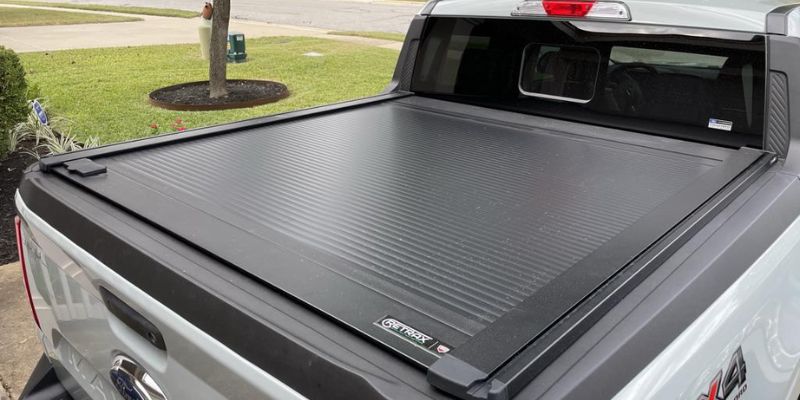
While installing the Retrax PowertraxONE XR requires precision and attention to detail, several critical alignment issues can arise during the setup process.
Common installation complications include improper rail positioning and insufficient clamp tension, which can lead to water leakage and operational inefficiencies.
To address these alignment fixes, users should implement strategic measures during installation.
Utilizing scrap wood and clamps helps achieve ideal rail-to-cover fitment, while ensuring the bed rail clamps are properly torqued prevents unwanted gaps.
Critical inspection points include verifying foam seal placement and condition throughout the assembly process.
Additionally, checking truck bed levelness before installation prevents water pooling issues that could compromise the cover’s integrity.
Proper alignment during setup considerably reduces the likelihood of subsequent operational problems and water intrusion concerns.
Maintenance Requirements and Repair Solutions
To maintain ideal performance of the Retrax PowertraxONE XR, owners must implement a systematic maintenance routine that addresses key components and potential wear points.
The maintenance protocol requires regular cleaning of rails and tracks to prevent debris accumulation that could compromise smooth operation.
Critical maintenance tasks include applying appropriate lubricants to moving parts and the opening mechanism, which preserves functionality and prevents rust formation.
Weather resistance depends on intact seals, necessitating prompt replacement of damaged components to maintain protection against water intrusion.
Regular inspection of hardware tightness and cover alignment ensures peak performance and prevents operational issues.
For effective maintenance, owners should strictly adhere to manufacturer guidelines, utilizing mild soap and water solutions for cleaning to preserve the cover’s integrity and extend its service life.
FAQs
What Are the Problems With Retrax?
Common issues include retract mechanism failures, water leakage around seals, installation misalignment challenges, durability problems with motor components, and warranty concerns regarding repair coverage. Regular maintenance required for peak performance.
How Do You Lubricate a Retrax Bed Cover?
Like a well-oiled machine, proper lubrication requires applying silicone-based spray to clean side rails and canister components every few months. Avoid petroleum-based products, as they attract debris and compromise performance.
What Is the Difference Between Retraxone MX and XR?
The RetraxONE XR features aluminum construction and 500-pound capacity, while the MX uses polycarbonate with 250-pound limit. XR offers superior weather sealing and an advanced locking system compared to MX’s basic mechanism.
Is the Retrax XR Waterproof?
The Retrax XR is not fully waterproof. While featuring water drainage systems and weather-resistant cover materials, seal maintenance is critical. Testing shows water intrusion can occur during severe conditions, particularly around rail and tailgate areas.
Final Thoughts
Like Achilles’ vulnerable heel, the Retrax PowertraxONE XR’s potential issues require vigilant diagnostics and maintenance protocols.
Critical evaluation of seal integrity, rail alignment calibration, and motor functionality guarantees peak performance.
Systematic inspection of waterproofing components and electrical systems, combined with proper torque specifications during installation, mitigates common operational failures.
Regular preventive maintenance protocols remain essential for sustained system reliability.