The BAKFlip Fibermax is a popular truck bed cover that many truck owners enjoy.
It’s known for its sleek look and how well it works. But like any product, it’s not perfect. Some people have run into problems with it.
If you have one or are thinking about getting one, this article is for you.
I’m going to talk about the most common issues people have faced and how to fix them.
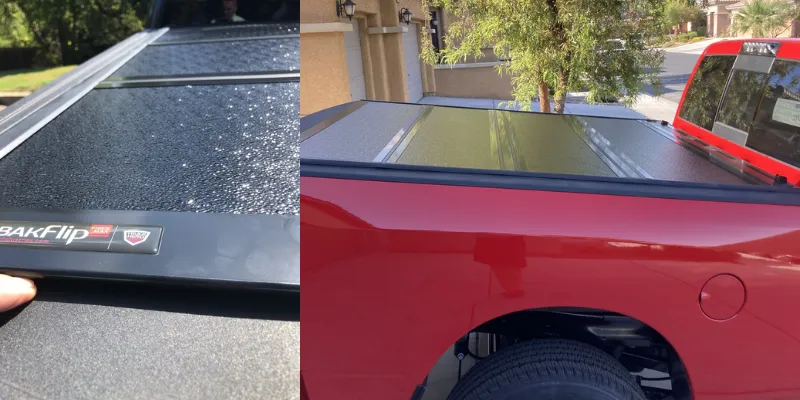
BAKFlip Fibermax Cover Common Problems and Solutions
1. Poor Fit and Alignment Issues
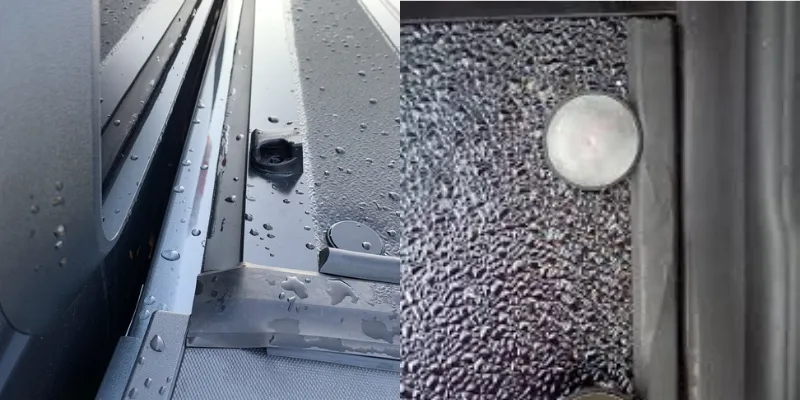
One of the biggest complaints about the BAKFlip Fibermax is that it doesn’t always fit right. This can cause a bunch of problems:
Gaps Between Panels
Some truck owners notice spaces between the panels when the cover is closed. This not only looks bad but can also let water in and make your truck less secure.
To fix this:
- First, check all the mounting hardware. Make sure every bolt and screw is tight. Sometimes, things can come loose during shipping or installation.
- Next, look at the side rails. They might need adjusting. The cover should sit snug against them.
- Finally, make sure the cover is lined up right with your truck bed. It should be centered and even on all sides.
If you’ve done all this and still see gaps, you might need to adjust the tension on the cover.
There are usually tension adjusters at the front of the cover. Try tightening or loosening these a bit to see if it helps close the gaps.
Cover Not Sitting Flat
Another common problem is when the cover doesn’t lay flat on the truck bed, especially at the front or back. This can let water in and make the cover less effective.
Here’s what to do:
- First, double-check the installation instructions. Make sure you didn’t miss any steps.
- Look at the front and back seals. They might need adjusting. These seals should press firmly against your truck bed when the cover is closed.
- If the front isn’t sitting right, check the bump stops. These are small rubber pieces that the cover rests on. They might need adjusting.
- For issues at the back, look at how the cover meets the tailgate. There should be a good seal there.
If none of this works, it’s time to call BAKFlip customer service. They might have some model-specific tips to help you out.
2. Leaks and Inadequate Waterproofing
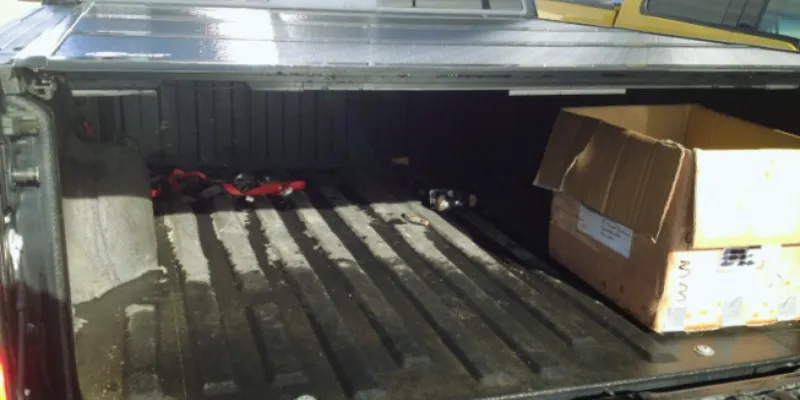
Water getting into your truck bed is a big problem. It can ruin your cargo and even lead to rust. Here’s how to deal with leaks:
Finding Leak Sources
Water can sneak in through several places:
- Between the panels
- Along the sides where the cover meets the truck bed rails
- At the front or back of the cover
To stop the leaks:
- Start by doing a water test. Spray your truck with a hose and look for where water is getting in.
- Check all the seals. Look for any that are worn out, cracked, or not sitting right. Replace any bad seals.
- Look at the hinges between panels. Sometimes water can get in here.
- Check the drain tubes. These should guide water out of the truck bed. Make sure they’re not clogged or kinked.
Improving Overall Waterproofing
If you’re still having leak problems, try these steps:
- Use a high-quality silicone sealant on the seams. Be careful not to get it on any moving parts.
- Add extra weatherstripping in problem areas. You can buy this at most auto parts stores.
- Consider using a water-repellent spray on the whole cover. This can add an extra layer of protection.
- Look at how the cover meets the bulkhead (the front of the truck bed). Sometimes adding an extra seal here can help a lot.
Remember, no truck bed cover is 100% waterproof. But with these steps, you can get pretty close.
3. Parts Coming Loose or Falling Off
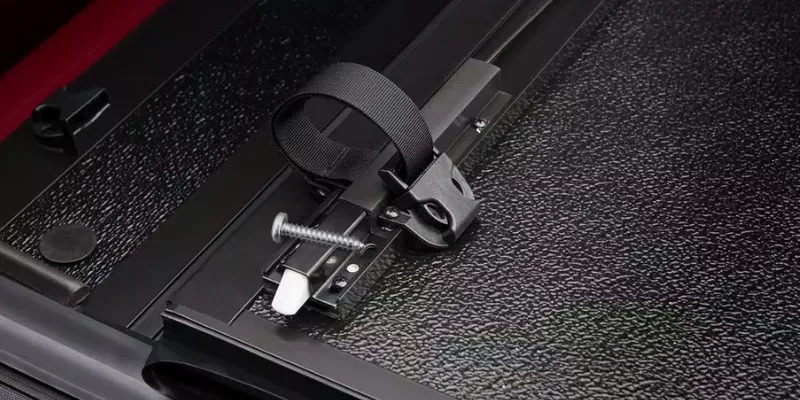
It’s frustrating and dangerous when parts of your cover start falling off. Here’s how to deal with this:
Common Parts That Come Loose
- Latching bars: These help keep the cover closed and secure.
- Panel hinges: They allow the panels to fold.
- Rail clamps: These attach the cover to your truck bed.
To fix this:
- Regularly check all screws, bolts, and clamps. Tighten anything that’s loose.
- Use thread-locking compound on bolts and screws. This is a special glue that keeps screws from coming loose due to vibration.
- If you notice any stripped screws or damaged parts, replace them right away.
Preventing Future Issues
To stop parts from coming loose in the future:
- Don’t overload the cover. It’s not designed to hold a lot of weight.
- Be gentle when opening and closing the cover. Slamming it can loosen parts over time.
- Do a quick check of all parts every month or so. This can help you catch problems early.
- If you use your truck off-road, check the cover more often. Rough terrain can shake things loose.
4. Easily Scratched Surface
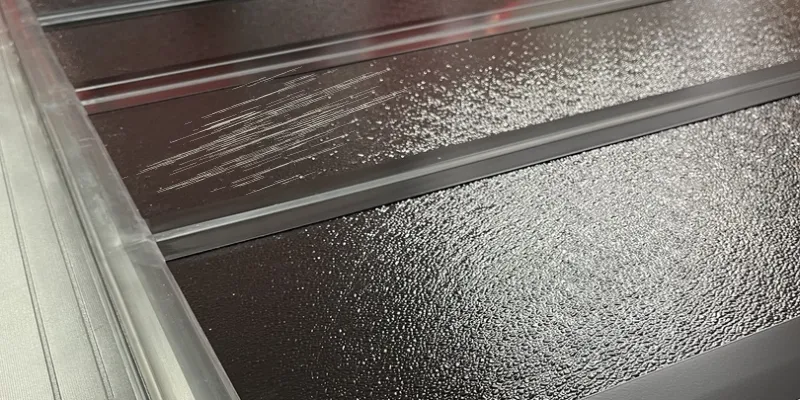
The BAKFlip Fibermax looks great when it’s new, but it can get scratched up pretty easily. Here’s how to deal with this:
Preventing Scratches
- Be extra careful when loading and unloading your truck. Try not to slide things across the cover.
- Use a rubber mat or blanket when putting things on top of the closed cover.
- Don’t put sharp or rough objects directly on the cover.
- Consider applying a clear protective film to high-wear areas. This is like the screen protector you might use on a phone.
Dealing with Existing Scratches
- For light scratches, try using a plastic polish. You can find this at most auto parts stores.
- If the scratch is a bit deeper, you might be able to use a scratch repair kit. These usually come with a filler and a polish.
- For really deep scratches, you might need to replace the panel. Contact BAKFlip to see if you can buy individual panels.
Remember, some scratches are just part of using your truck. Try to think of them as giving your truck character!
5. Difficulty Latching and Unlatching
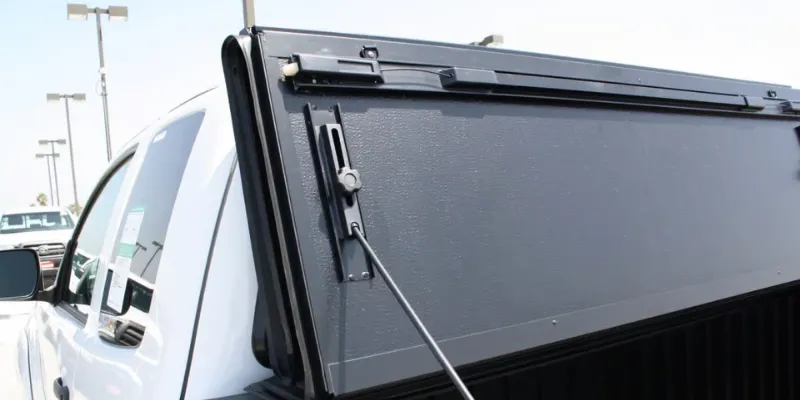
A cover that’s hard to open or close can be really annoying. Here’s how to make it work smoothly:
Common Latching Issues
- Sticky or hard-to-move latches
- Latches that don’t line up right
- Broken latch mechanisms
To fix these:
- First, clean the latches. Sometimes dirt and grime can make them sticky.
- Use a dry silicone spray on all moving parts. Don’t use WD-40 or other wet lubricants, as these can attract dirt.
- Check the alignment of the latches. They should line up perfectly when you close the cover.
- If a latch is broken, you’ll need to replace it. You can usually order replacement parts from BAKFlip.
Adjusting Latches
- Most BAKFlip covers have adjustable latches. Look for small screws or bolts near the latch.
- If the cover is hard to close, try loosening the latch mechanism a bit.
- If the cover doesn’t feel secure when closed, you might need to tighten the latch.
- Always make small adjustments. A quarter turn of a screw can make a big difference.
6. Quality Control Problems
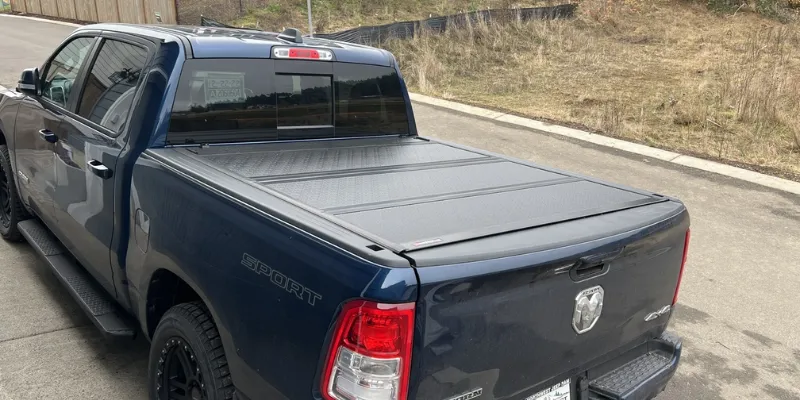
While BAKFlip is known for good quality, sometimes problems slip through. Here’s what to look out for:
Identifying Quality Issues
- Misaligned pre-drilled holes: This can make installation really hard.
- Inconsistent panel thickness: The panels should all be the same thickness.
- Poor finish or visible defects: Look for bubbles in the finish or rough edges.
What to do:
- As soon as you get your cover, inspect it carefully. Don’t install it if you see problems.
- Take clear photos of any issues you find.
- Contact BAKFlip customer service right away. They should be able to send you replacement parts or a whole new cover if needed.
Dealing with Factory Defects
- If you’ve already installed the cover and then notice a defect, document it with photos.
- Check your warranty. Most quality issues should be covered.
- Be persistent with customer service. Sometimes you might need to escalate your complaint to get it resolved.
7. Installation Challenges
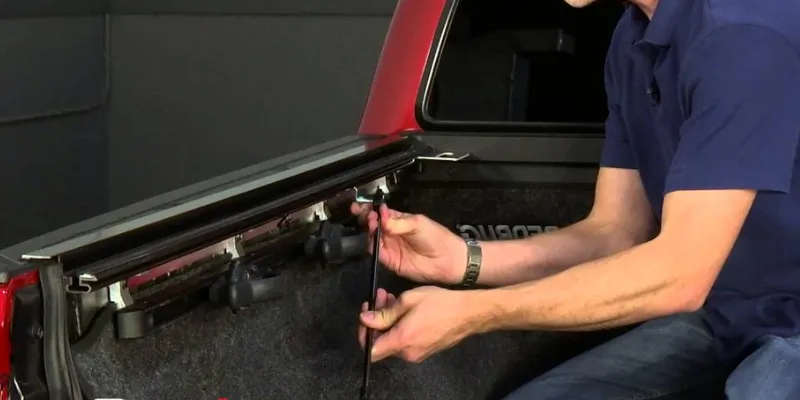
Many people find installing the BAKFlip Fibermax harder than they expected. Here’s how to make it easier:
Common Installation Hurdles
- Vague or confusing instructions
- Difficulty aligning the cover properly
- Problems with the rail clamping system
Tips for a Smooth Installation:
- Before you start, read through all the instructions. Then read them again.
- Watch installation videos online. Sometimes seeing it done makes it clearer.
- Lay out all your parts before you start. Make sure you have everything.
- Get a friend to help. An extra set of hands can make a big difference.
- Take your time. Rushing can lead to mistakes.
Troubleshooting Installation Problems
- If the rails don’t seem to fit, double-check that you have the right model for your truck.
- For alignment issues, start over from the beginning. Sometimes a small mistake at the start can cause big problems later.
- If you’re really stuck, don’t force anything. Call BAKFlip customer support or consider professional installation.
8. Heat-Related Issues
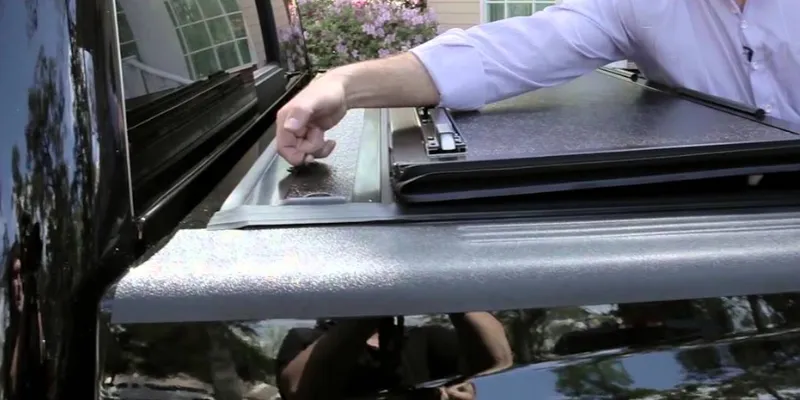
Hot weather can cause several problems for the BAKFlip Fibermax. Here’s what to watch out for:
Adhesive Failure
High heat can cause adhesives to fail, leading to parts coming loose.
To prevent and fix this:
- When possible, park in shaded areas or use a truck cover.
- If you notice any parts coming loose, clean the area thoroughly.
- Use a heat-resistant adhesive for repairs. You can find these at auto parts stores.
- In some cases, you might want to use mechanical fasteners (like screws) in addition to adhesives.
Hot Panels
The cover’s surface can become extremely hot in direct sunlight, making it uncomfortable or even dangerous to touch.
To deal with this:
- Always use gloves when handling the cover on hot days.
- If possible, let the cover cool before folding or unfolding it.
- Consider applying a heat-reflective coating to the cover’s surface. This can help reduce heat absorption.
- If the heat is causing the cover to warp, contact BAKFlip. This might be covered under warranty.
9. Short or Inadequate Rails

Some users find that the rails provided with their BAKFlip Fibermax are too short for their truck bed. This can cause a host of problems, from poor fit to leaks.
Addressing Rail Length Issues
- First, double-check that you have the correct model for your truck. Sometimes people accidentally order the wrong size.
- Measure your truck bed and compare it to the specifications for your BAKFlip model.
- Contact BAKFlip to verify rail specifications. They might have sent the wrong rails by mistake.
- If the rails are indeed too short, ask BAKFlip about getting replacement rails of the correct length.
Solutions for Short Rails
- In some cases, you might be able to use rail extensions. These can give you the extra length you need.
- If BAKFlip doesn’t offer a solution, consider checking with aftermarket suppliers. Some make compatible rail extensions.
- As a last resort, a skilled mechanic might be able to modify the rails to fit. But be aware this could void your warranty.
10. Foam Seals Blowing Out
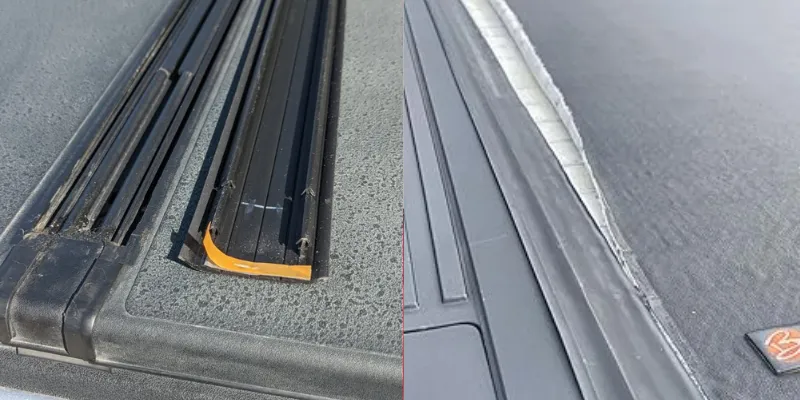
The foam seals play a crucial role in keeping water out, but they can deteriorate or blow out over time. This is especially common in areas with extreme temperatures or lots of sun.
Preventing Seal Damage
- Avoid slamming the cover closed. This can compress and damage the seals over time.
- Regularly clean the seals with a mild soap and water solution. This removes dirt that can wear them down.
- Apply a UV protectant to the seals every few months. This can help them last longer, especially in sunny climates.
- When washing your truck, avoid spraying high-pressure water directly at the seals.
Replacing Blown-Out Seals
- You can usually buy replacement seals directly from BAKFlip or an authorized dealer.
- Before applying new seals, clean the surface thoroughly with rubbing alcohol.
- When installing new seals, start at one end and work your way along, pressing firmly to ensure good adhesion.
- Consider upgrading to higher-quality aftermarket seals for improved durability. Some companies make seals specifically designed to withstand extreme conditions.
11. Cable Release Mechanism Problems
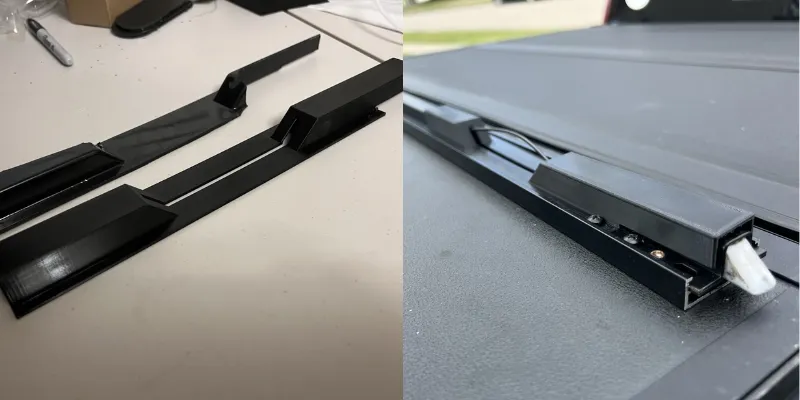
The cable release system is designed to make opening the cover easy, but it can sometimes cause frustration.
Common Cable Issues
- Frayed or broken cables
- Cables coming loose from attachment points
- Difficulty engaging or disengaging the release
Solutions:
- Regularly inspect the cables for signs of wear. Look for fraying or kinks.
- If a cable is frayed, replace it immediately. Don’t wait for it to break completely.
- Ensure the cables are properly routed. They shouldn’t be rubbing against any sharp edges.
- Lubricate the cable mechanisms with a dry lubricant. Avoid wet lubricants as they can attract dirt.
- If the release is hard to engage, check the cable tension. It might need adjusting.
Adjusting Cable Tension
- Most BAKFlip models have a way to adjust cable tension. Check your manual for the exact location.
- If the release feels too loose, try tightening the cable slightly.
- If it’s too hard to pull, try loosening it a bit.
- Make small adjustments. A little goes a long way with cable tension.
Remember, if you’re not comfortable working with the cable system, it’s best to contact a professional. Improperly adjusted cables can make your cover unsafe to use.
Final Thoughts
The BAKFlip Fibermax cover is a popular choice for many truck owners, and for good reason. It offers a sleek look and great functionality.
However, like any product, it’s not without its challenges. By being aware of these common issues and their solutions, you can make an informed decision about whether this cover is right for you.
If you already own a BAKFlip Fibermax, these tips should help you maintain and troubleshoot your cover effectively.
Remember, regular maintenance and prompt attention to small issues can prevent larger problems down the road.
With proper care, your BAKFlip Fibermax can provide years of reliable service for your truck.