Operating a Gator MT utility vehicle requires understanding its common mechanical vulnerabilities.
These machines exhibit distinct patterns of failure that operators must recognize and address proactively.
From primary clutch assemblies to drive train components, specific wear points demand regular inspection and maintenance protocols.
The following analysis identifies critical failure modes and their corresponding solutions, providing essential knowledge for maximizing vehicle uptime and performance reliability.
Primary Clutch Sticking Issues
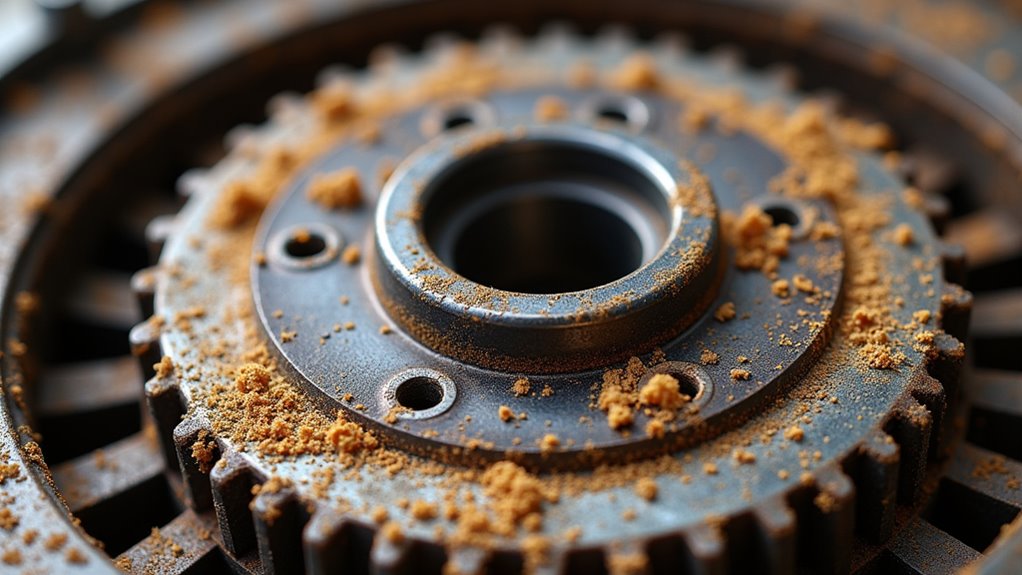
Primary clutch sticking plagues Gator MT models when shifting between drive positions, manifesting as resistance or complete binding during gear changes.
This mechanical impediment typically intensifies as operating temperatures rise, creating a compounding effect that can severely impact transmission functionality.
To maintain operational autonomy and prevent costly repairs, operators must implement proactive maintenance protocols.
Regular inspection of the primary clutch assembly helps identify potential binding points, accumulated debris, or wear patterns that could trigger sticking issues.
Proper lubrication serves as a critical preventive measure, ensuring smooth clutch engagement and disengagement.
Neglecting primary clutch sticking issues can cascade into more severe transmission complications, potentially resulting in extended vehicle downtime and substantial repair expenses.
Swift diagnosis and remediation of clutch binding symptoms protect both mechanical integrity and operational efficiency.
Shifting Mechanism Failures
While closely related to primary clutch issues, shifting mechanism failures in Gator MT models present distinct operational challenges that require specific diagnostic and remedial approaches.
These failures manifest primarily through difficulty altering between gears, particularly when shifting from Neutral to drive positions.
Temperature fluctuations during operation can greatly impact shifting mechanism performance, potentially accelerating wear patterns within the transmission system.
When shifting mechanism failures occur, operators typically experience increased resistance during gear changes, which can cascade into more severe transmission complications if left unaddressed.
Preventative maintenance protocols focusing on the shifting assembly are essential for maintaining peak functionality and avoiding costly repairs.
Regular inspection and servicing of the shifting mechanism components help guarantee smooth operation and extend the vehicle’s service life, ultimately preserving the Gator MT’s operational integrity.
Fluid Leakage and Maintenance
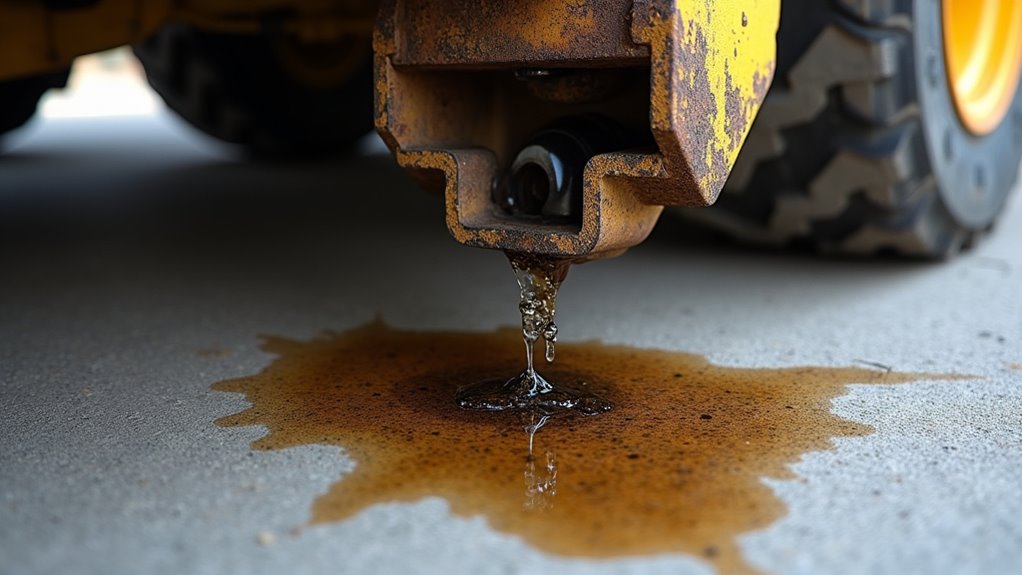
Proper fluid maintenance protocols represent a critical aspect of Gator MT operational integrity, with systematic monitoring and preventive measures essential for averting mechanical failures.
The maintenance regimen necessitates vigilant inspection of seals and connections to identify early indicators of fluid leakage, which often signals underlying system deterioration.
Regular assessment of oil condition prevents gas dilution and potential engine damage, while monitoring fluid levels helps regulate operating temperatures during vehicle operation.
Critical maintenance procedures include examining CV boots and bearing assemblies for wear-induced leakage points.
These preventive measures greatly reduce the risk of mechanical failures and enhance vehicle longevity.
Implementing a thorough fluid maintenance schedule, adhering to manufacturer specifications, enables operators to maintain peak performance while minimizing the likelihood of costly repairs and unexpected downtime.
Power Mount Electrical Problems
Electrical system failures in the Motorguide Gator Power Mount represent a significant operational challenge, extending beyond routine maintenance concerns.
Members of the Gator Tail Nation frequently encounter short circuits and system failures due to inadequate motor sealing and water intrusion.
Component | Common Issue |
---|---|
Motor Housing | Water infiltration |
Circuit Board | Short-circuit damage |
Gear Assembly | Power-related wear |
Limit Controls | Missing switches |
Replacement Parts | Limited availability |
The absence of limit switches compounds the electrical problems, often resulting in mechanical jamming that further stresses the system.
With the product’s discontinuation, sourcing replacement electrical components has become increasingly difficult for owners seeking to maintain their power mounts.
The combination of water-damaged motors and gear failures creates a cascade of electrical issues that compromise the mount’s reliability and performance.
Gear System Breakdowns
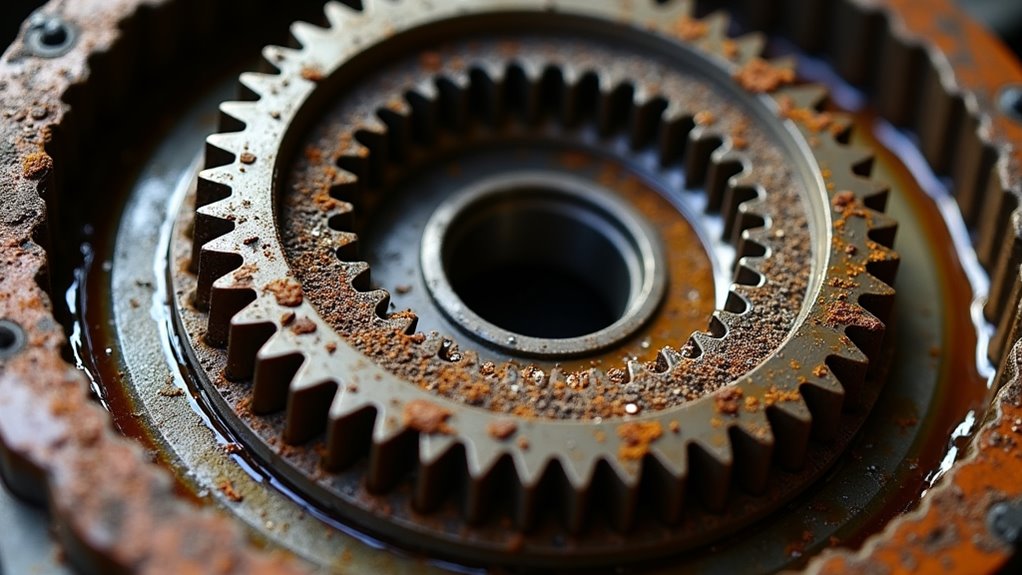
Deteriorating gear systems in Gator MT units manifest through multiple failure modes, primarily stemming from insufficient lubrication protocols and maintenance deficiencies.
Critical indicators include compromised gear engagement, often resulting from misaligned or damaged teeth structures within the transmission assembly.
System performance degradation frequently presents through primary clutch sticking mechanisms, which greatly impact gear-shifting capabilities and overall operational efficiency.
The combination of inadequate temperature management and mechanical stress accelerates component wear, particularly when operating under high thermal loads.
To mitigate gear system breakdowns, operators must implement systematic inspection protocols, focusing on bearing integrity and fluid level optimization.
This preventative approach guarantees sustained functionality while minimizing the risk of catastrophic failures that could render the equipment inoperable.
Mounting Bracket Wear and Tear
Beyond gear system integrity, mounting bracket degradation represents a considerable concern for Gator MT operators.
These critical components face substantial stress from sustained operational loads and environmental exposure, potentially leading to misalignment issues that compromise equipment stability.
Deterioration manifests through visible defects including structural cracks, deformation, and corrosion development.
When mounting brackets exhibit these warning signs, immediate replacement becomes imperative to prevent cascading equipment failures.
Implementation of preventive maintenance protocols, including systematic inspections and proper lubrication schedules, considerably extends bracket longevity.
Additionally, utilizing protective coatings or weatherproof covers provides an effective defense against environmental factors that accelerate wear.
These proactive measures guarantee ideal bracket performance while maintaining the equipment’s operational reliability and safety standards throughout its service life.
Weather Seal Deterioration
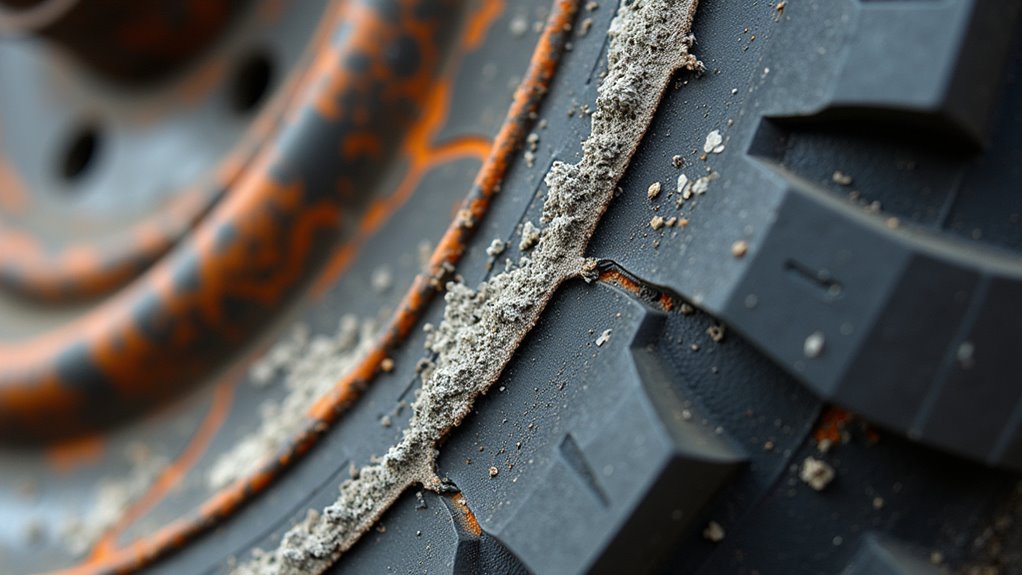
Integrity of weather seals plays a critical role in safeguarding Gator MT equipment from environmental infiltration and operational disruption.
When weather seal deterioration occurs, water intrusion can compromise sensitive electrical and mechanical components, leading to system failures and reduced performance reliability.
Operators should monitor for telltale indicators of seal degradation, including visible cracks, separation points, and peeling along seal surfaces.
Environmental stressors, particularly UV exposure and thermal cycling, accelerate the deterioration process, necessitating vigilant inspection protocols.
While replacement seals are available through authorized distribution channels, their specialized nature often commands premium pricing compared to standard automotive alternatives.
Implementation of systematic maintenance schedules, incorporating regular seal condition assessments, proves essential for preventing moisture-related complications and maintaining peak equipment functionality, especially during adverse weather operations.
Drive Belt Performance Issues
Maintaining ideal drive belt performance stands critical to the reliable operation of Gator MT systems.
Drive belt performance issues commonly manifest through slippage, reduced acceleration, and compromised power transfer, potentially leading to cascading mechanical complications if left unaddressed.
Industry experts recommend systematic inspection protocols to detect early warning signs such as fraying, cracking, or improper tensioning.
Under demanding operational conditions, particularly in construction environments, drive belts typically require replacement between 1,000 and 1,500 miles of service.
This preventative maintenance approach safeguards against unexpected failures and guarantees optimal system functionality.
Replacement costs range from $50 to $150, varying by model specifications and supplier selection.
Proactive monitoring and timely replacement of deteriorating drive belts represent essential practices for maintaining peak vehicle performance and preventing costly downtime.
Bearing and Joint Complications
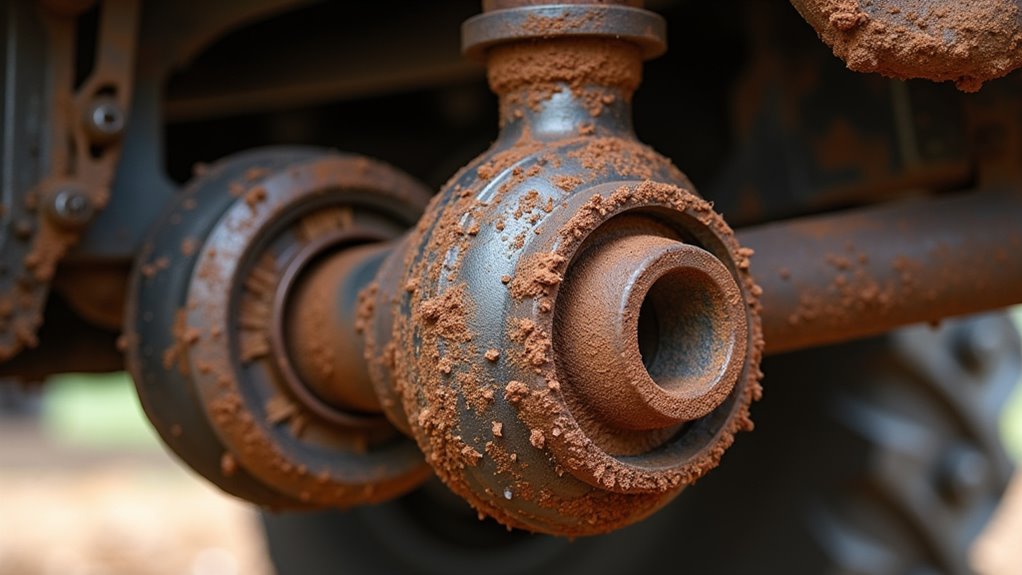
While drive belt issues often command immediate attention, bearing and joint complications represent equally important mechanical concerns in Gator MT systems.
Loose bearings frequently emerge as a primary wear point, generating excessive friction that can cascade into system-wide mechanical deterioration if left unchecked.
Essential maintenance protocols should focus on CV boot integrity, as compromised boots allow contaminants to infiltrate important joint assemblies.
The primary clutch system requires particular scrutiny, as inadequate lubrication can result in bearing strain and compromised shifting performance.
Regular joint alignment inspections are essential to prevent accelerated bearing wear and premature component failure.
Maintenance documentation plays an essential role in tracking bearing replacement patterns and joint repair history, enabling operators to anticipate potential complications and implement preventive measures before important failures occur.
Temperature-Related Malfunctions
Temperature fluctuations pose considerable operational challenges for Gator MT systems, particularly during extended periods of use in adverse conditions.
Temperature-related malfunctions manifest across multiple system components, impacting overall performance and longevity.
Component | Temperature Effect |
---|---|
Transmission | Compromised gear shifting |
Fluid Systems | Reduced oil viscosity |
Electrical | Degraded wire connections |
These thermal variations can trigger a cascade of operational issues, from transmission overheating to compromised lubrication efficiency.
Critical concerns include clutch wear acceleration and drive belt deterioration under sustained high-temperature conditions.
When exposed to moisture, the electrical system’s vulnerability increases greatly, particularly when combined with elevated temperatures.
Performance enhancement requires implementing targeted preventive measures, including regular fluid monitoring and systematic component inspection protocols.
Operators must remain vigilant for early warning signs of temperature-related malfunctions to maintain ideal system functionality.
FAQs
How Many Hours Will a John Deere Gator Last?
Operational longevity factors indicate John Deere Gators typically achieve 5,000-10,000 service hours. Performance metrics vary based on maintenance protocols, environmental conditions, and utilization patterns, with proper care maximizing unit lifespan potential.
How Reliable Are John Deere Gators?
John Deere Gators demonstrate high reliability when proper maintenance protocols are followed. With systematic service intervals and proactive component replacement, these utility vehicles consistently deliver peak performance across demanding operational environments, maximizing return on investment.
How Do I Make My John Deere Gator Go Faster?
Like releasing a caged beast, speed modifications for Gators include performance air intakes, ECU tuning, high-flow exhaust systems, upgraded drive belts, and weight reduction. These enhancements can greatly boost horsepower and acceleration capabilities.
What Kind of Transmission Does Gator Have?
John Deere Gators utilize a Continuously Variable Transmission (CVT) system, featuring belt-driven technology that delivers seamless power distribution and infinite gear ratios.
This transmission type enables peak performance across diverse operating conditions.
Final Thoughts
Technical awareness and proactive maintenance protocols remain paramount for ideal Gator MT performance.
Like a well-oiled machine, these vehicles demand systematic attention to their critical components—from clutch assemblies to electrical systems.
Implementation of regular diagnostic procedures, coupled with preventive maintenance schedules, considerably mitigates operational failures and extends service life, ensuring maximum uptime and operational efficiency in field conditions.